Helmet safety specialists MIPS (multi-directional impact protection system) is opening its virtual testing tool to the wider market to help brands’ research and design. H&H speaks to MIPS and manufactuers to find out what this means for riders and the market
ADVANCES in virtual helmet testing are hoped to push hat safety forwards at new speed, while helping keep costs down.
The progress concerns finite element analysis (FEA) tools, which allow engineers and developers to simulate real-world testing on virtual products. While FEA tools are not new, how they are being used in helmet design – and who has access to them – has taken a sizeable step forwards.
Helmet safety specialists MIPS (multi-directional impact protection system) announced in October it is opening its virtual testing tool to the wider market to help brands’ research and design.
MIPS’s FEA testing service allows testing of helmets virtually in accordance with a range of safety standards.
MIPS chief executive Max Strandwitz told H&H the company started FEA modelling in 2002 and has used it for a lot of experimental testing and technology development, but this marks the public launch of openly offering that capability to brands.
“It’s early days, we’ve run a couple of projects with simulation and brands think it’s fantastic because they can see how a helmet will perform before it exists,” said Mr Strandwitz, explaining MIPS offers FEA testing on the rotational element of protection rather than just compression.
“That’s the complicated part, because all of a sudden you have the movement, a certain angled impact.
“Our commitment is to make the world a little bit safer, so we need to bring this to the market. We will start small with a couple of brands, but my ambition is to roll this out to a lot of others. It is a fantastic tool. From a sustainability point of view you don’t need to go into trial and error, you can develop helmets a lot faster, you know you will have a safer result, so I think it’s a win-win in most aspects.”
Alex Burek, of Charles Owen which has been working with MIPS for five years, told H&H this development is “very exciting”.
She said tools such as FEA allow prototypes to be tested more quickly, giving faster insights into potential improvements.
“In short, the faster we can interpret development data, the quicker we can make bigger leaps in equestrian safety within our in-house innovation lab, which will save more lives when products are brought to market,” she added.
Champion Hats also took a major step this year in opening its state-of-the-art testing laboratory.
This brought tools to aid development and improve the safety of Champion’s products in-house, which it had been using as part of its five-year collaboration with the University of Cardiff.
These include FEA modelling of shell compression and optimisation as well as 3D printing of scaled helmet shells and FEA verification of these.
A Champion spokesman said the firm is “proud to be the first organisation” to bring the testing tools in house, and has recruited three engineers, who all have vast experience in FEA, computer-aided design and 3D printing.
“We look forward to providing a bright new safe future for all our customers as our reputation is built on it,” she added.
You might also be interested in…
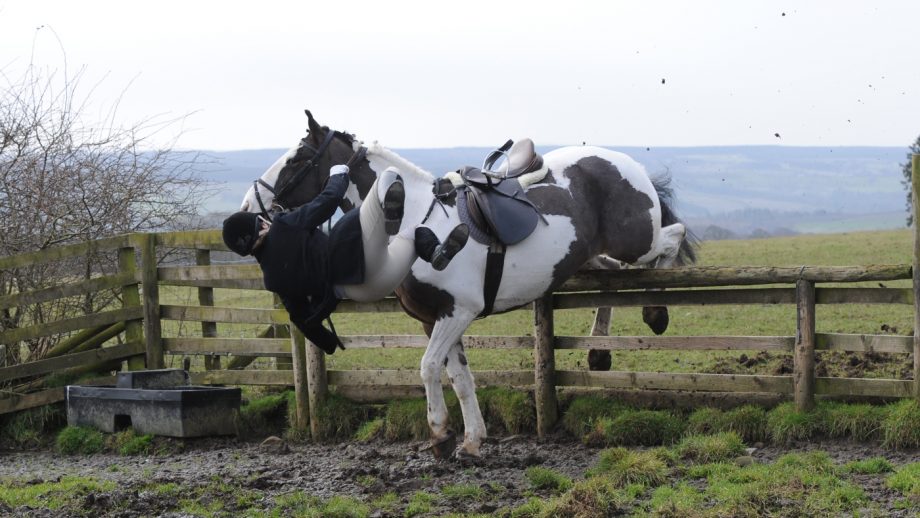
Education could help riders make the right hat choices *H&H Plus*
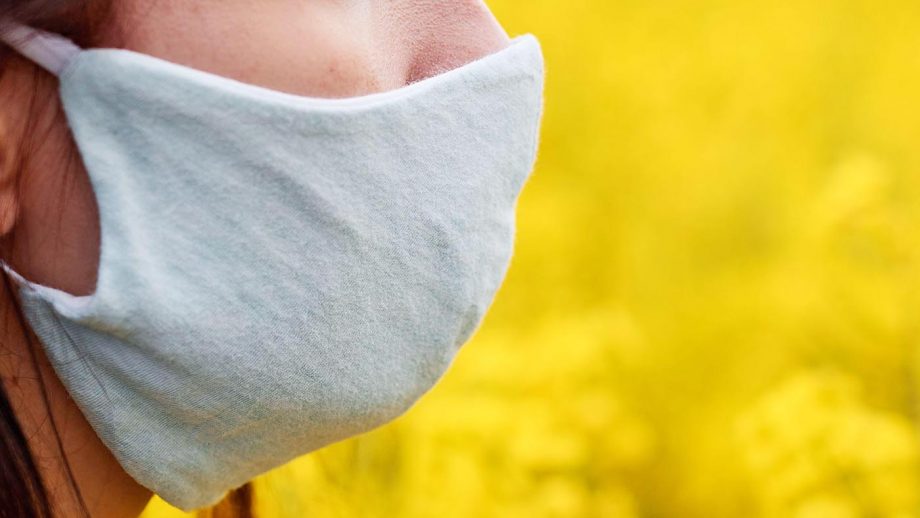
‘No grey areas’: equestrians warned to comply with coronavirus rules or risk consequences
FEI medical committee chairman Dr Mark Hart reminded equestrians they cannot ‘just apply what we want and ignore what is
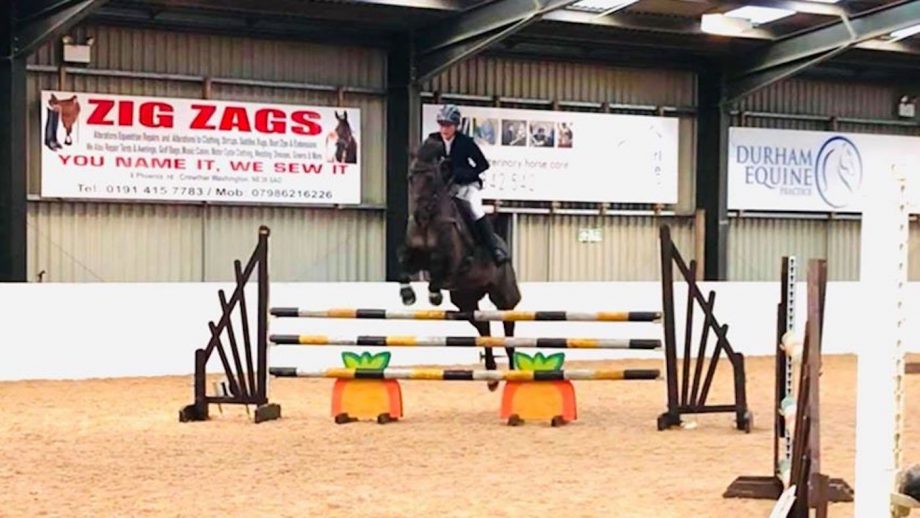
‘You’ve only got one head’: coach’s hat warning after surviving six-inch gash to her face
‘Sometimes people save their best hats for competitions, but they should be wearing them at home too’
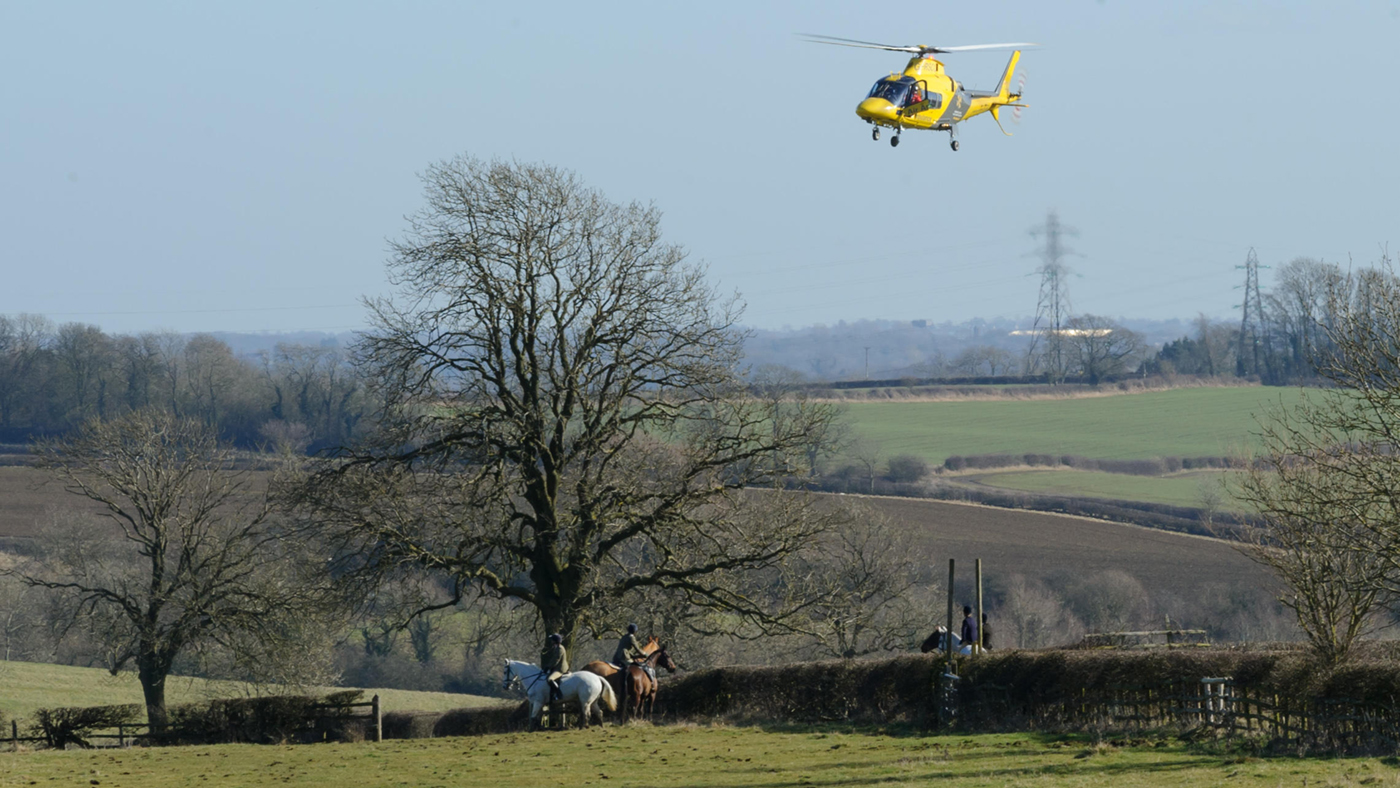
Safety in horse sport: the latest statistics and innovations *H&H Plus*
Equestrianism will always be a high-risk sport, but horse and rider injury rates are decreasing. H&H assesses the latest safety
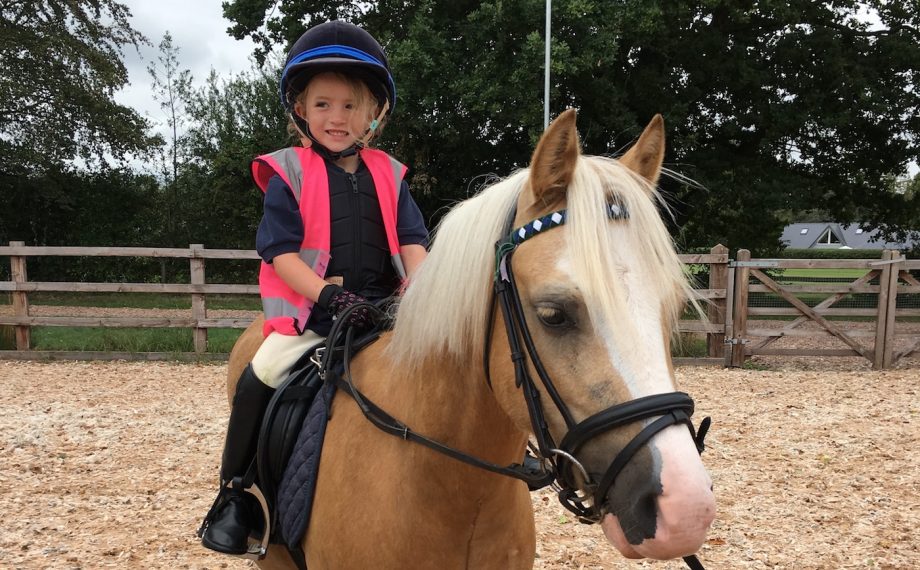
Five-year-old girl falls on the road after pony spooked by cycle event
‘Some of these cyclists seem to just ride along, heads down, with no thought of any consequences’